
Your Plastic Foam and Film Densifier Company
AD-60 SERIES

Specifications:
Application: Foam & Film trim/waste
Material types: PE, EPE, EPP and EPS
Inlet Type: Dual Shaft High
Torque Shredder
Inlet Size: 21.5” X 19-1/2”
Feed Rate: 0 to 200(pounds per hour)
Brick Mold Size: 4”x 12”x 24”
​Dimensions: 76”L x 38”W x 75”H (approx)
Voltage: 460-3-60 or 220-1-60
Weight: 1,200 lbs. (Approx.)
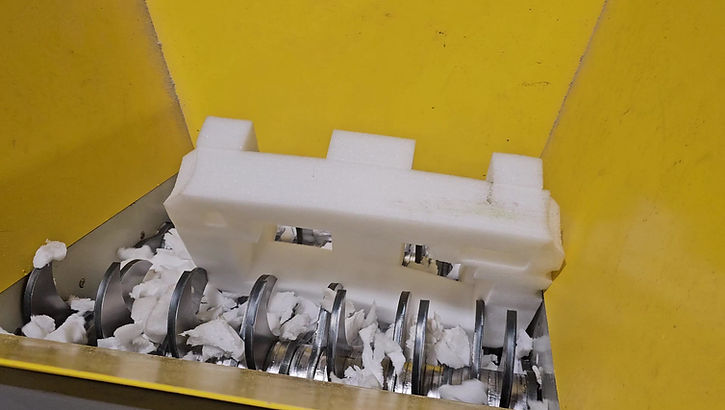
JTW shredders are designed and built for rugged operation. Tough materials such as EPE and EPP are easily processed through our dual shaft design. Heavy duty spherical bearings are standard, and the shafts are each driven by direct-coupled gearmotors.


AD-60 HD SERIES
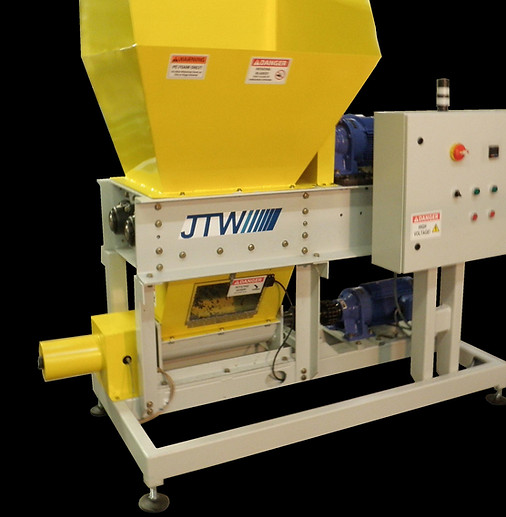
Specifications:
Application: Foam & Film trim/waste
Material types: PE, EPE, EPP and EPS
Inlet Type: Dual Shaft High
Torque Shredder
Inlet Size: 28” X 29-1/2”
Feed Rate: 0 to 200(pounds per hour)
Brick Mold Size: 4”x 12”x 24”
​Dimensions: 83”L x 48”W x 81”H (approx)
Voltage: 460-3-60 or 220-1-60
Weight: 1,200 lbs. (Approx.)
AD-60 D SERIES

Specifications:
Application: Foam & Film trim/waste
Material types: PE, EPE, EPP and EPS
Inlet Type: Dual Shaft High
Torque Shredder
Inlet Size: 28” X 29-1/2”
Feed Rate: 0 to 400(pounds per hour)
Brick Mold Size: 4”x 12”x 24”
​Dimensions: 83”L x 48”W x 81”H (approx)
Voltage: 460-3-60 or 220-1-60
Weight: 2,200 lbs. (Approx.)

Exhaust Ventilation System
Exhaust Ventilation SystemThis system attaches to the material discharge of the densifier and pulls non-toxic but unpleasant fumes out of the work area and conveys them outside the work area. Fan outlet ductwork is provided by others and not provided in this quotation. This system consists of the following items:
​
-
1.5 HP Blower
-
Starter Panel
-
Exhaust hood for AD60 Hopper
-
Exhaust hood for AD60 Purge Die
-
Flexible tubing from hoods to Blower
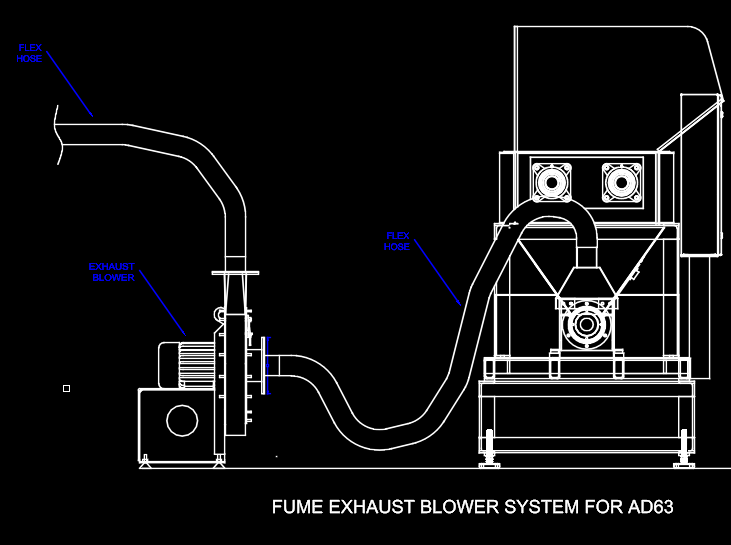
Theory of Operation:
Foam sheet, planks and cut-outs can be compressed into rigid, high bulk-density logs that can be easily handled or stacked. Converting foam to up to 30 lbs./ft3 bulk weight, the AC compactor provides a clean and efficient method to handle scrap and significantly reduce disposal or transportation costs. Employing a patent pending compacting technology, the AC compresses foam scrap into a square log. The outer surface of the log is heated, creating a thin, rigid outer shell that maintains the brick shape. logs are continuously pushed out and cut to a preset length, adjustable from 8” to 48”, making it possible to palletize and ship the scrap affordably. Unlike baling systems, no strapping is required, dust and debris are reduced, and the logs can be fed directly into most grinders or shredders for recycling.
Easy to Install and Operate
With one 3-phase power connection and a pneumatic attachment, the compactor can be ready in five minutes. Simple controls, powered by a central PLC, insure that even the most inexperienced operator can run the KP in no time.
Our Compactors can be operated in-line with an extrusion or converting system, or with remote receiver for bags, cut-outs and other flexible loose scrap. The compactors can be mounted on castors, enabling mobility around the plant or recycling area.
Foam Scrap "Auger Densifier" (AD)
Reduce disposal costs and increase profits by converting your foam scrap into a manageable and recyclable product with the AD series scrap densifier / melter.Features:•Simple and quick to install and start up.•Safe, quiet, clean and efficient operation.•Minimal floor space required.•Produces bricks that are easy to handle and stack. No baling wire required.•Works with clean or dirty materials.•Up to 90:1 densification. Permit up to 40,000 lb loads on 40’ containers. •Works with EPS, PE Foam, EPE and EPPReduce Costs & Increase Profits:•Bin Rental, Hauloff & Landfill Fees•Floor Space Usage•Housekeeping/Labor•Sell Densified Scrap to Recyclers•Increase Ship Weight per Truckload
Shredder: JTW shredders are designed and built for rugged operation. Tough materials such as EPE and EPP are easily processed through our dual shaft design. Heavy duty spherical bearings are standard, and the shafts are each driven by direct-coupled gearmotors.